
Structural Health Monitoring
Introduction
- What is Structural Health Monitoring and Response?
Methodology & Technology
- Why employ SHM?
- What are the advantages of SHM?
Our Solutions
- GMS series recorders for distributed and hybrid systems
- CR series modular multichannel recording systems for central and hybrid systems
- A wide variety of high quality sensors to measure acceleration, velocity, displacement, strain, tilt and environmental phenomena
- Software solutions with highly customisable options
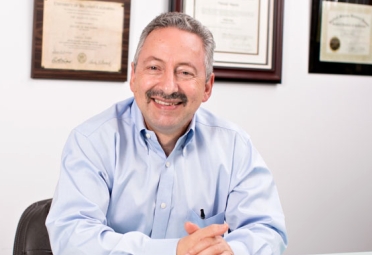
Structural Analysis Consultancy
With some complex structures, due to size or shape, it is more difficult to determine which instruments are needed or where they should be installed for efficacy. However, expert structural analysis is available.
GeoSIG — through a strategic alliance with Dr. Farzad Naeim, an internationally renowned expert in structural health monitoring — can offer consultancy and turnkey solutions for structural health monitoring of all types of structures including high-rise buildings, public buildings, bridges, tunnels and other special structures.
Using the expertise of the highly respected Dr. Farzad Naeim, who boasts over 35 years' experience and publications ranging from textbooks to journal papers, you can have peace of mind that your structure is safely surveyed and the most reliable solution is specified.
GeoSIG, with more than 30 years' expertise in structural monitoring solutions, can fulfil the requirements of the most challenging structure. Click here to visit his Website, or look over the solutions leaflet to see what we can offer.
GeoSIG — through a strategic alliance with Dr. Farzad Naeim, an internationally renowned expert in structural health monitoring — can offer consultancy and turnkey solutions for structural health monitoring of all types of structures including high-rise buildings, public buildings, bridges, tunnels and other special structures.
Using the expertise of the highly respected Dr. Farzad Naeim, who boasts over 35 years' experience and publications ranging from textbooks to journal papers, you can have peace of mind that your structure is safely surveyed and the most reliable solution is specified.
GeoSIG, with more than 30 years' expertise in structural monitoring solutions, can fulfil the requirements of the most challenging structure. Click here to visit his Website, or look over the solutions leaflet to see what we can offer.
- What is Structural Health Monitoring and Response?
Sometimes called SHM, SHRM or S2HM, Structural Health Monitoring and Response (SHM) is an innovative method of monitoring structural status and performance without otherwise affecting the structure itself. SHM utilises several types of sensors embedded in—or attached to—a structure to detect exceedance of allowed performance criteria as well as to identify and verify structural behaviour.
Methodology & Technology
- Why employ SHM?
Instrumentation of a structure will depend on the type of structure being monitored, its uses, its physical characteristics, etc, so an SHM solution for a bridge will look different than an SHM solution for a high-rise building. However, the principle remains the same: sensors are strategically placed on the structure and are connected to a recorder. As the data comes in and is recorded, it is sent to software that analyses the data and compares it to predetermined performance parameters. When there are significant enough exceedances, notification, alerts or alarms are triggered.
- What are the advantages of Structural Health Monitoring and Response?
The ideal GeoSIG SHM system provides the end user with on-demand information about their structure’s measured features, as well as warnings concerning any exceedance detected. Therefore SHM also significantly reduces repair costs through early damage detection, making the monitored structure safer and increasing the cost efficiency of its maintenance. This is why SHM can significantly reduce insurance premiums for those operating or overseeing the safety of infrastructure such as bridges, railways or tunnels. SHM provides increased understanding of in-situ structural behaviour and decreased down-time for inspection and repair.
Further reading
We have more information on this topic in the form of a scientific paper entitled, "Black Box Concept Can Help Promote Widespread Use of S2HM," which can be found here and in our Downloads section.
We also have two informational videos, also available on our YouTube channel: